基于离散元+有限元+多体动力学+流体,本文对某斗轮式堆取料机进行仿真,分析点:
1. 磨损分析,2. 跑偏分析,3. 洒料分析,4. 效率分析,5. 能耗分析,6. 斗轮体受力分析,7. 悬臂梁受力分析。
1. 磨损分析
在斗轮堆取料机设备中,主要磨损区域分别为斗体、导流板以及受料皮带机,其中斗体中的斗齿和斗唇磨损最为严重。
影响因素:挖掘的物料种类/比重、粒径大小、物料形状、进给量以及旋转速度等。
如图所示为斗体的法向累积接触能和切向累积接触能。
1.1 斗体法向累积接触能和切向累积接触能
2. 跑偏分析
由于斗轮体空间结构的限制,导致物料落至受料皮带机时不居中,以及物料对受料皮带的冲击力的大小和方向,引起皮带两侧的应力不对称,久而久之造成了皮带跑偏。
影响因素:导流板结构(角度和形状,影响了物料冲击力的方向)、物料密度、输送运量(影响了料流的冲击力的大小)等,
如图所示,通过物料冲击方向、物料冲击区域以及物料质量分布等方式来分析物料对受料皮带的冲击情况以及受力分析,快速识别出是否存在跑偏的问题。
2.1 物料冲击方向
2.2 物料冲击区域
2.3 物料质量分布
3. 洒料分析
洒料主要可能发生在斗体取料、斗体卸料以及物料落至皮带的过程。其中,斗体卸料是由于物料较粘或者斗轮旋转速度较大时,导致物料在斗体内未能及时卸料,而从斗轮后方滑落。
影响因素:斗轮旋转速度、物料粘性、物料大小等。
可以直接通过软件来观察物料在设备运行过程中料流轨迹来判断是否存在洒料现象。
3.1 料流轨迹
4. 效率分析
指单位时间内斗轮所挖取到物料量,主要可以通过分析斗容和受料皮带运量的方式分析。对于前文中所描述的洒料问题和堵料问题,还可以通过斗体内物料的预留情况和停留时间来分析。
影响因素:斗轮旋转速度、进给量、斗体结构、物料粘性/堵料、洒料等。
斗容分析:如图所示,该斗轮在7.5s左右,开始进入料堆取料(因设置传感器较大,获取质量偏大),直至9s时取完物料并离开料堆时为真实斗容情况。
其中靠近斗唇的物料由于离心力作用被抛撒出来,可测量处出此时斗容为1100kg左右;在11.2s时,物料开始卸料,直至卸料完成。
4.1 斗容分析
受料皮带运量分析:如图所示,由于传感器放置的位置问题,从7.5s才获取到物料数据,即从7.5s到12.5s为靠近物料方向上的进给量所挖取的物料量,而从12.5s后趋于稳定,此时为水平方向进给,可以分析出这种进给量的情况下,斗轮机的运量大约为3000t/h。
4.2 受料皮带运量分析
5. 能耗分析
分析斗轮机在挖取物料过程中所需要的力矩(仅为斗轮对物料所需的力矩,未考虑斗轮自转、摩擦等损耗的能量)。
影响因素:旋转速度、进给量、物料密度、斗体结构等。
如图所示,设备在前11秒所需的力矩逐渐增加后趋于稳定,此时力矩为200000N.m左右。
5.1 斗轮对物料所需力矩分析
6. 斗轮体受力分析
如图所示,分别展示了斗轮体和斗齿在非作业/作业状态下的受力情况。
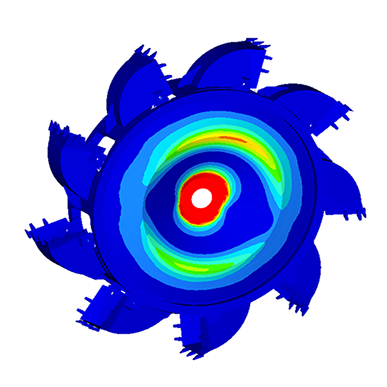
6.1 斗轮体非作业状态下受力分析 6.2 斗轮体作业状态下受力分析
7. 悬臂梁受力分
如图所示,分别展示了悬架在非作业/作业状态下的受力情况。
7.1 非作业状态下受力情况
7.2 作业状态下受力情况